Differences Between Vertical and Horizontal Multistage Pumps
Published:
Mar 10,2025
Multistage pumps are essential components in various industrial applications, designed to transport fluids at higher pressures than single-stage pumps. They achieve this by utilizing multiple impellers, or stages, each contributing to the overall pressure increase.

Multistage pumps are essential components in various industrial applications, designed to transport fluids at higher pressures than single-stage pumps. They achieve this by utilizing multiple impellers, or stages, each contributing to the overall pressure increase. This article explores the concept of vertical multistage pumps, their operational principles, and the distinctions between vertical and horizontal multistage pumps.
What is a Vertical Multistage Pump?
A vertical multistage pump is a type of centrifugal pump that incorporates multiple impellers arranged in a vertical stack. Each impeller, referred to as a stage, adds incremental pressure to the fluid as it passes through, resulting in a significant overall pressure increase. This design is particularly effective for applications requiring the movement of fluids over considerable distances or to elevated locations.
Key Features of Vertical Multistage Pumps:
- Space Efficiency: The vertical configuration minimizes the pump's footprint, making it ideal for installations where floor space is limited.
- High-Pressure Capability: By combining multiple stages, these pumps can achieve high-pressure outputs suitable for demanding applications.
- Operational Versatility: They are capable of handling various fluid types, including clean and slightly contaminated liquids, depending on the specific design and materials used.
Operational Principles:
In a vertical multistage pump, fluid enters the pump casing and is directed to the first impeller. As the impeller rotates, it imparts kinetic energy to the fluid, accelerating it outward. The high-velocity fluid then passes through a diffuser or volute, converting kinetic energy into pressure energy. This process occurs sequentially across all stages, with each impeller further increasing the fluid's pressure before it exits the pump.
Differences Between Vertical and Horizontal Multistage Pumps:
Orientation and Space Requirements:
Vertical Multistage Pumps: Designed with a vertical shaft orientation, these pumps require less horizontal space, making them suitable for installations with limited floor area.
Horizontal Multistage Pumps: Featuring a horizontal shaft orientation, these pumps typically require more floor space but may offer easier access for maintenance.
Installation and Maintenance:
Vertical Pumps: Installation is straightforward due to their compact design; however, maintenance can be more challenging, often requiring the removal of the motor and other components to access internal parts.
Horizontal Pumps: Generally easier to maintain, as components are more accessible, allowing for simpler inspection and servicing.
Operational Efficiency:
Vertical Multistage Pumps: Often exhibit higher efficiency levels due to their design, which can lead to energy savings in high-pressure applications.
Horizontal Multistage Pumps: While efficient, they may have slightly lower efficiency compared to vertical pumps, depending on the specific design and application.
Applications:
Vertical Pumps: Commonly used in applications requiring high-pressure fluid delivery and where space constraints exist, such as in high-rise building water systems and industrial processes requiring high-pressure fluid delivery.
Horizontal Pumps: Suitable for applications where space is less of a concern, and ease of maintenance is prioritized, such as in irrigation systems and industrial fluid transfer.
Structural Design:
Vertical Multistage Pumps: Typically feature a vertical casing that provides stability for both the motor and pump components.
Horizontal Multistage Pumps: Often have a horizontal casing design, which can influence the pump's footprint and integration into existing systems.
Conclusion:
Both vertical and horizontal multistage pumps are integral to various industrial applications, each offering unique advantages tailored to specific requirements. Vertical multistage pumps excel in space-constrained environments and high-pressure scenarios, while horizontal pumps are favored for their ease of maintenance and suitability for high-flow applications. Understanding these distinctions is crucial when selecting the appropriate pump configuration to ensure optimal performance and efficiency in your operations.
Keyword:
Previous
Recommended
May 28,2025
SHANGLISHI PUMP GROUP
Department Director: Ms. Wang
Tel: +86-311-82725800/82725629
Email: admin@sls-pump.com
WhatsApp: +86 15830676372
Mobile Website
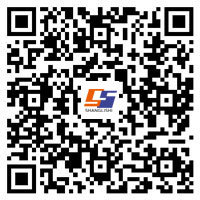
Mobile Website
Copyright © 2022 SHANGLISHI PUMP GROUP