How to Prevent Clogging in Submersible Sewage Pumps Handling Solid Waste
Published:
Jun 16,2025

How to Prevent Clogging in Submersible Sewage Pumps: 6 Proven Methods Saving 80% Repair Costs
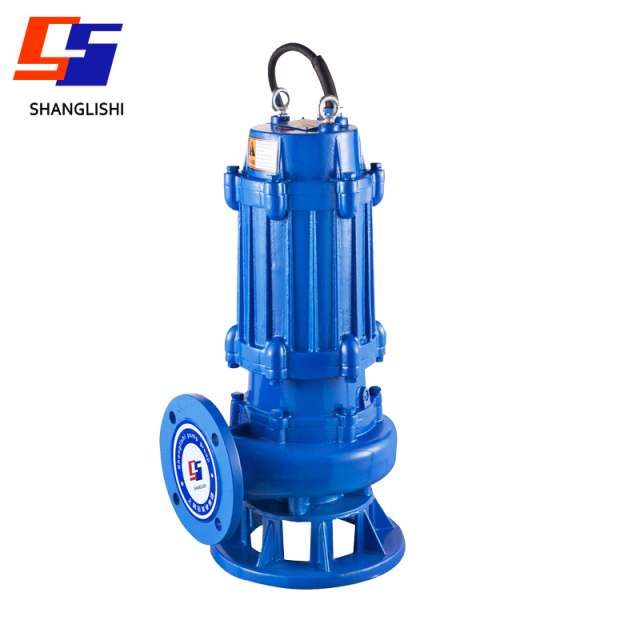
Clogged submersible sewage pumps cause 70% of pump failures in wastewater systems, leading to expensive downtime and repair bills. This guide reveals six field-tested methods to prevent solid waste buildup in your pumps. You'll learn how proper pump selection, preventive maintenance, and operational adjustments can extend pump lifespan by up to 5 years. Shanglishi engineers have documented these techniques through extensive testing in municipal and industrial applications. Discover how to maintain optimal flow rates while handling challenging solids like rags, plastics, and organic matter.
Why Sewage Pumps Clog: 3 Hidden Culprits
Understanding what causes clogs helps implement targeted prevention. These three factors contribute to 90% of pump blockages:
1. Solid Waste Accumulation
Debris like rags, plastics, and hair bind together inside pump chambers. In municipal wastewater, a single pump can process 200+ pounds of solids monthly. Without proper solids-handling capability, materials accumulate around impellers and seals.
2. Grease and Mineral Deposits
Fats solidify on internal components when pumps cool. Combined with mineral-rich water, these deposits reduce flow diameter by up to 60% within 6 months. Industrial facilities experience this most severely where oily wastewater enters the system.
3. Improper Pump Selection
Using pumps with undersized passageways causes immediate clogs. A recent case study showed a food processing plant reduced clogs by 75% after upgrading to pumps with 3" instead of 1.5" solids-handling capacity.
6 Effective Prevention Methods
1. Optimal Pump Selection
Choose pumps with ≥2" solids passage and specialized impellers. Cutting impeller designs shred rags and fibrous materials before they cause jams. Vortex impellers create water barriers that separate solids from critical components.
2. Install Inlet Protection
Bar screens or basket strainers capture large solids before they enter pumps. Opt for 10-15mm spacing between bars to balance protection and flow. Municipal plants using automatic rakes and dumpers reduce manual cleaning labor by 30 hours monthly.
3. Implement Source Control
Pre-treat wastewater to remove problematic materials. Food processors installing grease traps reduced pump maintenance frequency from weekly to quarterly. Educate staff about proper waste disposal - 40% of pump clogs originate from non-sewer items entering the system.
4. Schedule Regular Maintenance
Follow this maintenance timetable:
Frequency | Task | Clog Prevention Impact |
---|---|---|
After thick slurry use | Freshwater flush (20 minutes) | Prevents 85% of sediment buildup |
Every 300-500 hours | Oil change & seal inspection | Reduces failure risk by 60% |
Quarterly | Impeller clearance check | Maintains 95% flow efficiency |
Annually | Full tear-down inspection | Identifies wear before failure |
5. Optimize Operating Parameters
Adjust run times to prevent short cycling which causes debris accumulation. Install variable frequency drives to maintain ≥0.7 m/s flow velocity - the minimum required to keep solids moving. Pump stations optimized for continuous operation report 72% fewer blockages.
6. Install Monitoring Systems
Real-time sensors detect early warning signs like rising amp draw (indicates impeller resistance) or vibration increases. Systems triggering automatic shutdown during overload events prevent catastrophic clogs requiring complete disassembly.
Maintenance Techniques: Step-by-Step
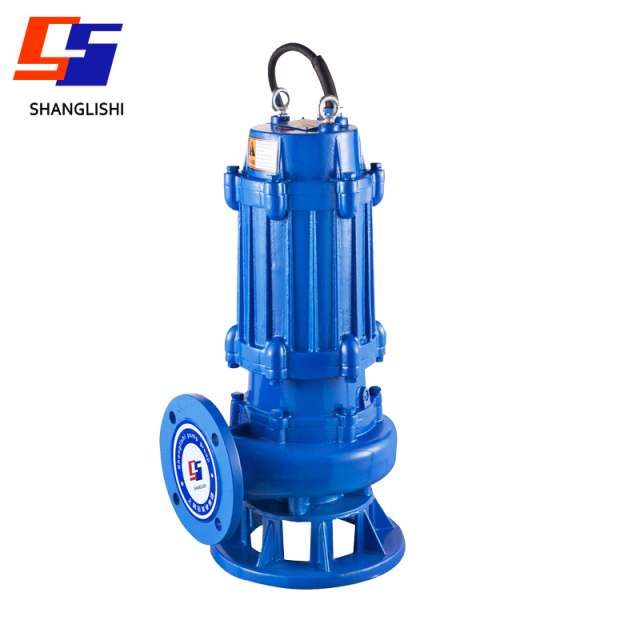
Critical Operation Guidelines
Proper operation prevents 35% of avoidable clogs:
Avoid Frequent Cycling
Limit starts to ≤6 per hour. Each restart pushes debris toward impellers. Install adequately sized wet wells to provide minimum 5-minute run times.
Prevent Dry Running
Low-water cutoff switches protect pumps from operating without sufficient cooling. Dry running causes thermal shock that warps impellers and creates ideal surfaces for debris accumulation.
Manage Fluid Levels
Maintain submersion depth ≥0.5 meters above pump inlets. This provides adequate pressure to push solids through rather than letting them settle around intake areas.
Anti-Clogging Technology Comparison
Technology | Clog Prevention Rate | Best Application | Maintenance Impact |
---|---|---|---|
Cutting Impellers | 85% | Fibrous waste (rags, hair) | Sharpen quarterly |
Vortex Impellers | 75% | Sandy/gritty environments | Annual inspection |
Grinder Pumps | 92% | High-solid concentration | Monthly checks |
Spherical Passages | 88% | Plastics & flexible solids | Biannual service |
Key Takeaways
Preventing clogs in submersible sewage pumps requires a systematic approach: Start with proper pump selection focusing on adequate solids-handling capability and clog-resistant impeller design. Implement inlet protection and source control to reduce problematic materials entering the system. Follow strict maintenance schedules with quarterly inspections and annual professional servicing. Optimize operations to maintain sufficient flow velocities and avoid destructive practices like frequent cycling. Install monitoring systems to detect issues before they cause complete blockages.
Facilities implementing these strategies report 80% fewer emergency callouts and extend pump service life by 3-5 years. For pumps specifically designed to handle challenging solids with minimal clogging risks, explore Shanglishi's clog-resistant sewage pump line featuring patented anti-clog technologies validated in 50+ industrial applications.
Keyword:
Recommended
May 28,2025
SHANGLISHI PUMP GROUP
Department Director: Ms. Wang
Tel: +86-311-82725800/82725629
Email: admin@sls-pump.com
WhatsApp: +86 15830676372
Mobile Website
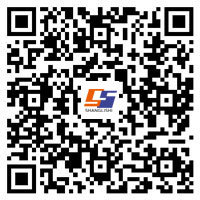
Mobile Website
Copyright © 2022 SHANGLISHI PUMP GROUP